Our Team
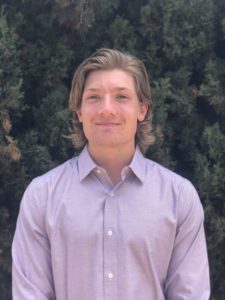
Aleksandr S. Breit
Aleksandr is a fourth year Aerospace Engineering student interested in pursuing higher education relating to structural analysis for aerospace applications. For his SURP project, he was responsible for designing the docking mechanism and simulating tests with finite element analysis. Aleksandr will be facilitating study sessions for various undergraduate classes during the 2021-22 academic year and will help as a TA for AERO 431 in the Spring.
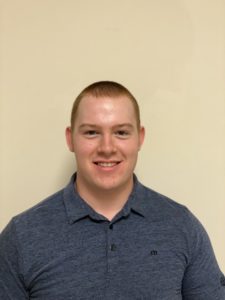
Samuel C. Maxwell
Samuel is a fourth-year mechanical engineering student. He intends to pursue a master’s degree in mechanical engineering with a focus on fluid mechanics and propulsion engineering. During SURP, Samuel performed analysis to compare the small and large drones and their thrust and ran simulations to study the disturbance caused by a docking maneuver and the associated response from the system.
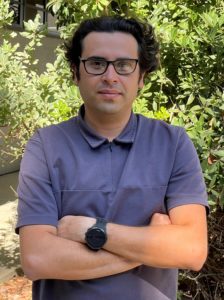
Behnam Ghalamchi
Behnam Ghalamchi received his doctorate degree in mechanical engineering from Lappeenranta University of Technology, Finland in 2014. From 2017 to 2019, he was a Postdoctoral Researcher at HiPeRLab, University of California, Berkeley, CA, USA. Since 2019, he is a Lecturer with California Polytechnic State University, San Luis Obispo, CA, USA.
Acknowledgements
We would like to thank the donors that have so graciously supported SURP. Without external support this project would not be possible. We also want to thank our mentor and advisor, Dr. Behnam Ghalamchi. His leadership was crucial to the progress this team made and setup for a continuation of this work in the future.
Our Project Video
Our Project's Digital Poster
Motivation
- Quadrotors are required to land in order to repair faulty components.
- Safe landing is often not feasible or is dangerous.
- Dysfunctional actuators can be replaced by attaching a smaller quadrotor mid-flight to provide the necessary torque and thrust values.
- Controlled flight can be resumed after connection is established, and the system is stabilized.
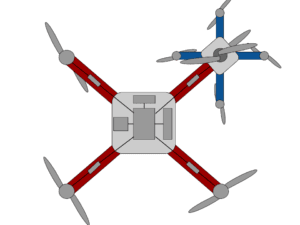
Mission Operations
- The small quadrotor aligns itself with the docking station.
- Neodymium magnets pull together the corresponding connections on the small and large quadrotors.
- Once secured, the dysfunctional motor-propeller system is powered down.
- Controls are re-routed to the top propeller attached to the small quadrotor.
- PID controllers reject the physical disturbances and resume stable flight.
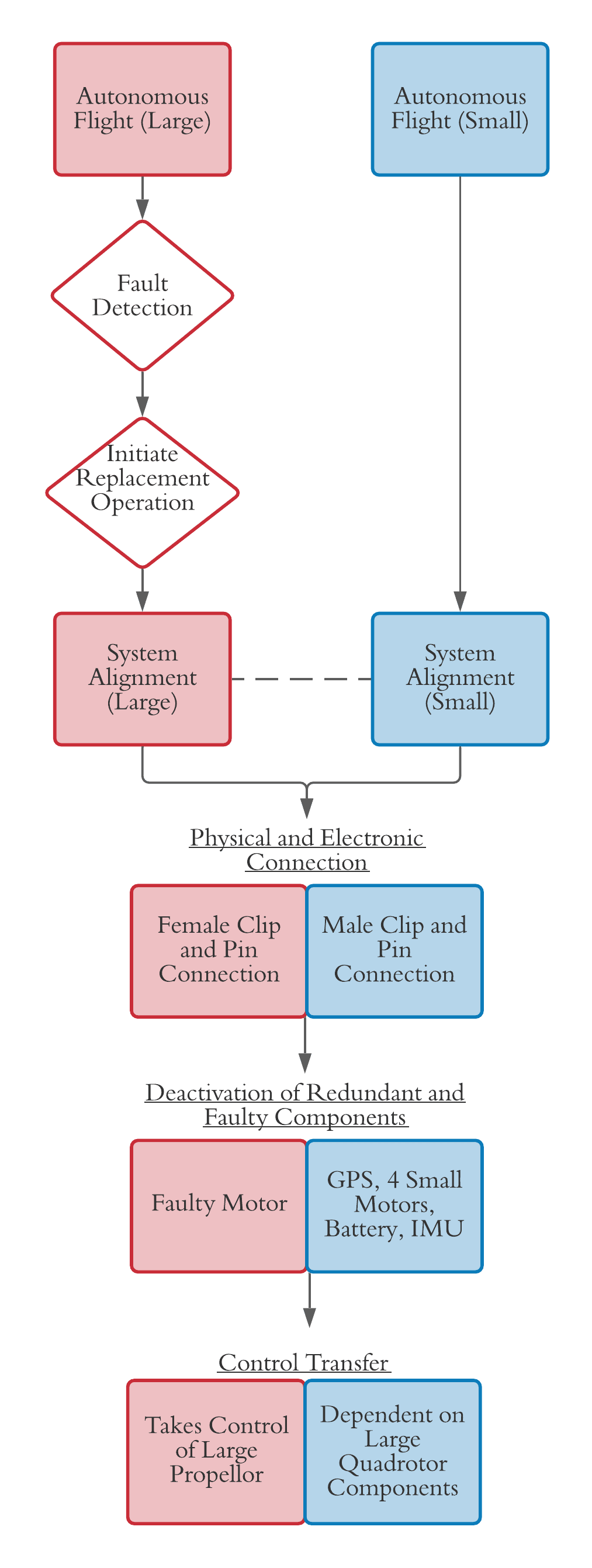
Connection Mechanism
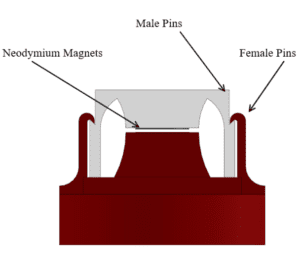
- Neodymium magnets provide the force required to deflect the pins on the large quadrotor docking component outwards.
- The small quadrotor docking component locks into place, establishing physical and electrical connection.
- The connection mechanism resists vertical and rotational displacement.
- Pogo pins activate once a sufficient downward force is applied.
- Two pins send and receive electrical charge while the third provides a voltage signal to control propeller rotation speed.
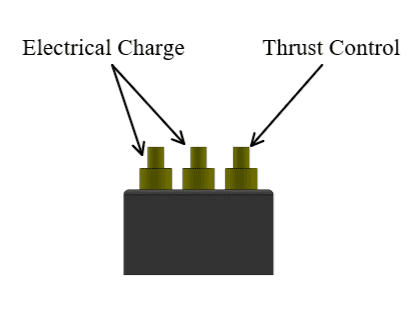
Finite Element Analysis
Finite element analysis was applied to the clip connection mechanism to test for failure under a realistic loading regime.
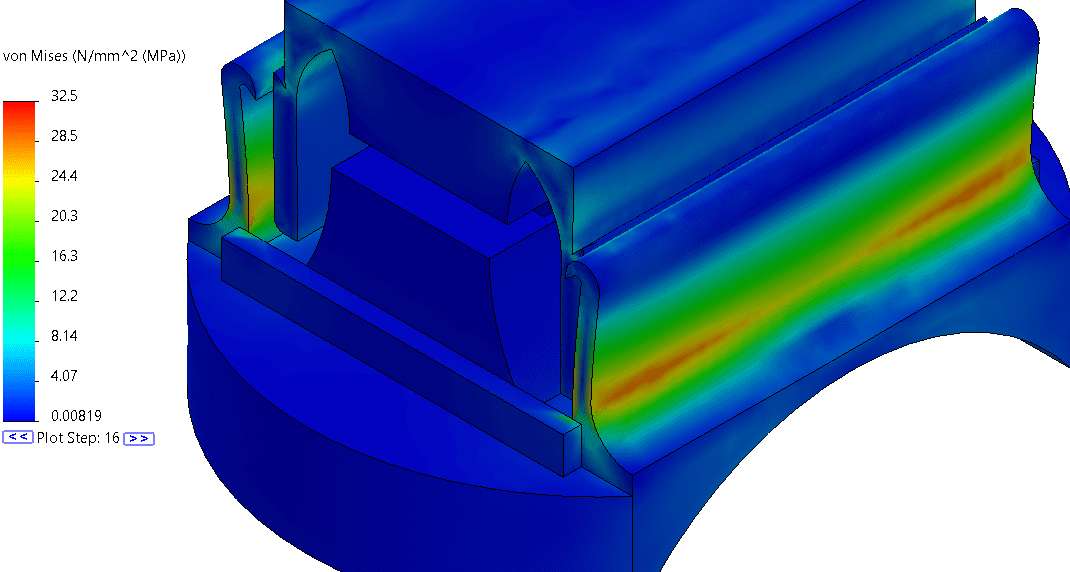
Maximum stress state:
- Maximum stress occurs simultaneously with the maximum deflection during the docking process.
- Analysis shows that the system does not fail under Von Mises failure criteria.
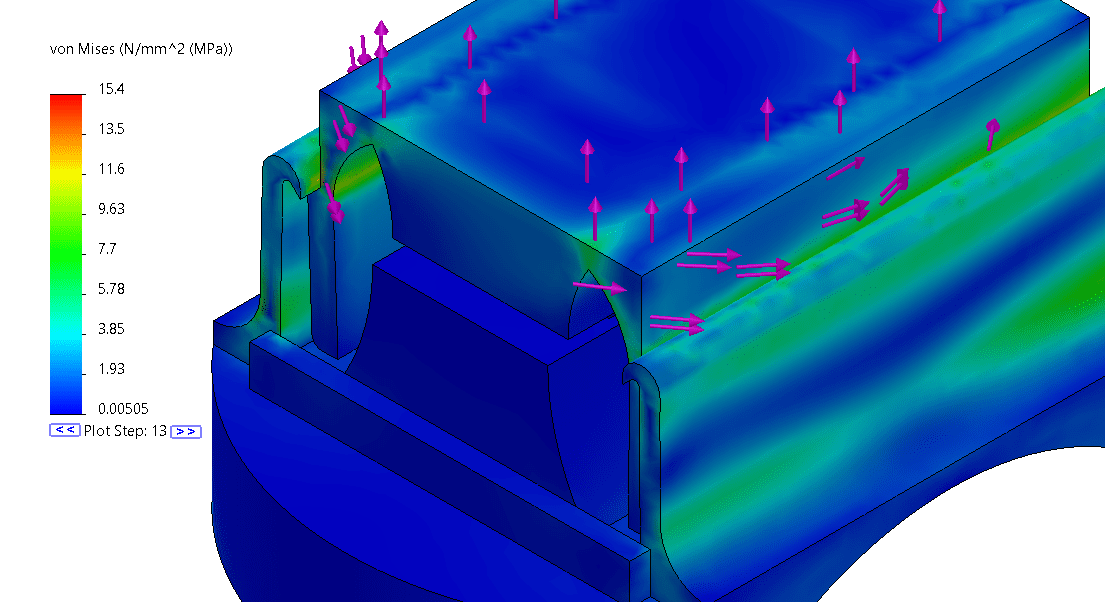
Combined loading:
- Clip connection stresses tested under a realistic vertical force and torque emulating the loads experienced during flight.
- The simulation showed the system resisted deformation and failure under the combined loading regime.
Disturbance Simulation
- A Simulink model was employed to study the control schemes of quadrotors.
- A disturbance acts on the arm of the faulty quadrotor.
- Disturbance imitates the expected forces due to the connection of both quadrotors.
- The PID controller was tuned to optimize the disturbance response.
- 3-D simulations were used to visualize system recovery from the disturbance.
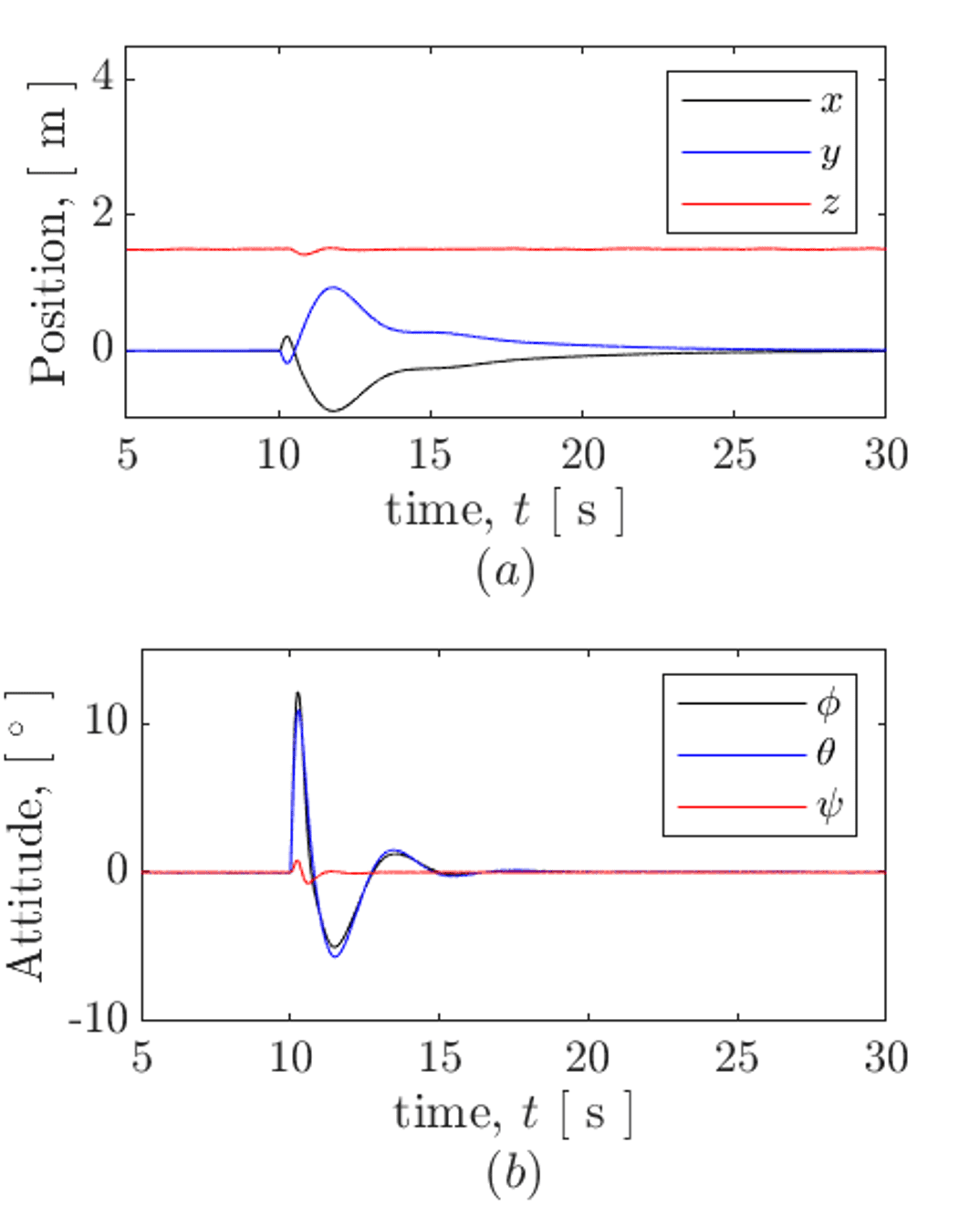
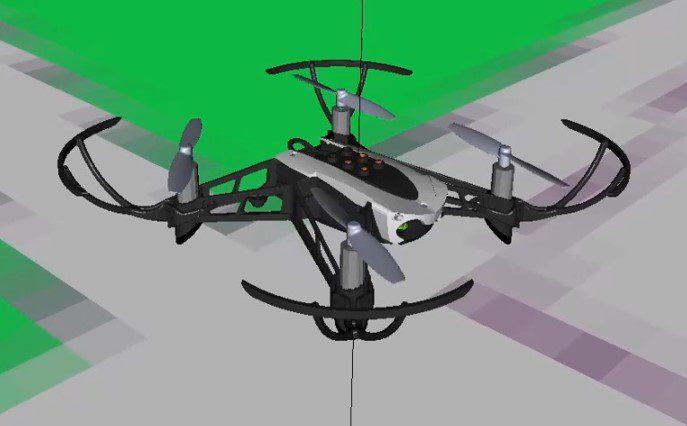
Conclusions
- Simulations show that the mechanical connection resists expected loading.
- The PID controllers reject the connection disturbances and can return the system to stable flight.
- Further work should design controllers to implement the small quadrotor’s four propellers rather than the attached fifth large propeller.
- Physical prototypes will be required to perform testing and data collection.
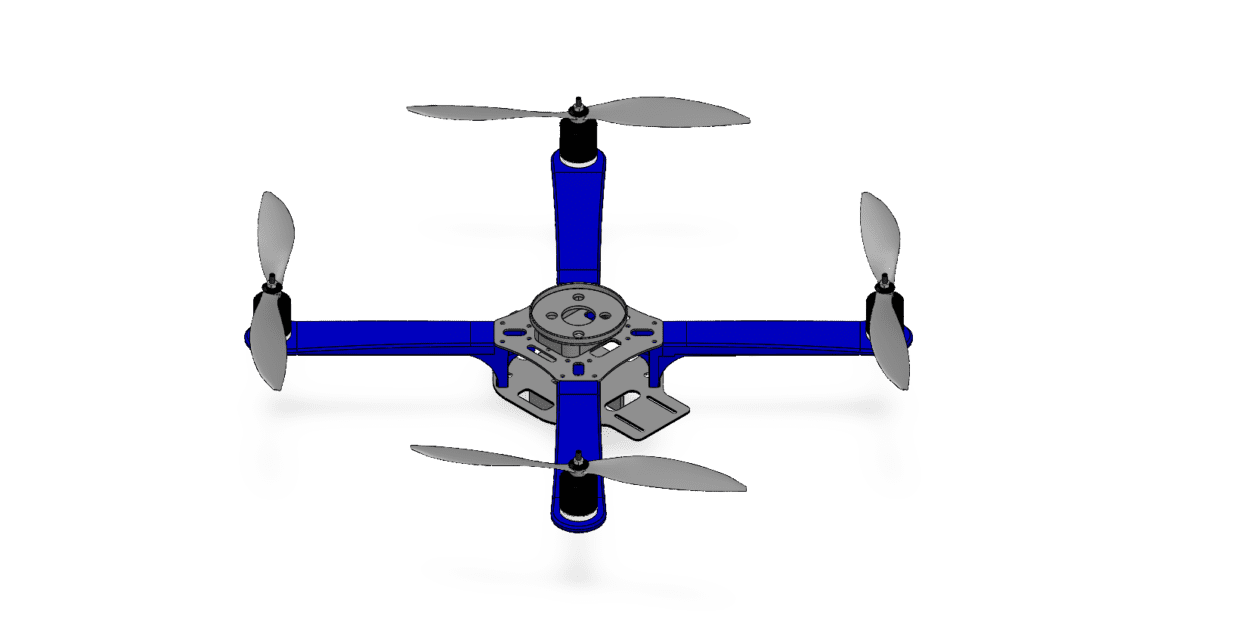